MKD Systems’ patented smart-servo-valve technology utilizes smart material, electrical feedback, and creative control technology to push forward the current state of art and deliver many key advantages, including but not limited to: highly resistance to fluid contamination, low leakage/power loss, free of null bias and shift, excellent low temperature performance, high bandwidth, and fewer number of failure modes.
A smart-servo-valve is a piezo-hydraulic servo valve powered by piezoelectric ring benders and a closed-loop electrical control system. More so, a piezo-hydraulic servo valve reduces mechanical wear and tear by removing the EHSV torque motor, flapper, and feedback spring and replacing by a pair of piezo ring-bender, so that the piezoelectric servo valve is substantially free of moving parts; whereby the assembly: replaces an electromagnetic torque motor and the transducer effect therefrom, with a pair of piezoelectric ring-bender that are mounted directly adjacent to a couple of nozzles; independently control the flow of fluid through the nozzles; replaces the flappers with the piezoelectric ring-bender; replaces the feedback spring that regulates the spool valve with a linear position sensing device that measures and provides feedback about the spool position to a valve controller, and a valve controller that allows the spool valve to move until the valve position achieves command position and the force on the spool valve is in equilibrium with the pressure difference across the spool valve; and forms an H-bridge where the pair of nozzles are the variable restrictors controlled by valve control software, generating a pressure difference across the spool valve when the piezoelectric bendable members bend away from the nozzle. A piezoelectric ring bender is a flat circular multilayer electro-ceramics disk that deforms in a concave or convex fashion depending on the polarity of the applied voltages.
The smart-servo-valve technology pushes forward the current state of the art in the following ways.
- Utilize smart-material as an electrical-to-mechanical transducer in place of an electromagnetic torque motor
- Utilize a pair of piezoelectric ring bender independently restricts the flow of a couple of nozzles instead of a flapper, driven by the torque motor, differentially regulating the flow from a pair of nozzles.
- Employ a closed-loop electrical control system using spool position feedback to achieve robust and precise servo valve control in place of mechanical force feedback through feedback spring.
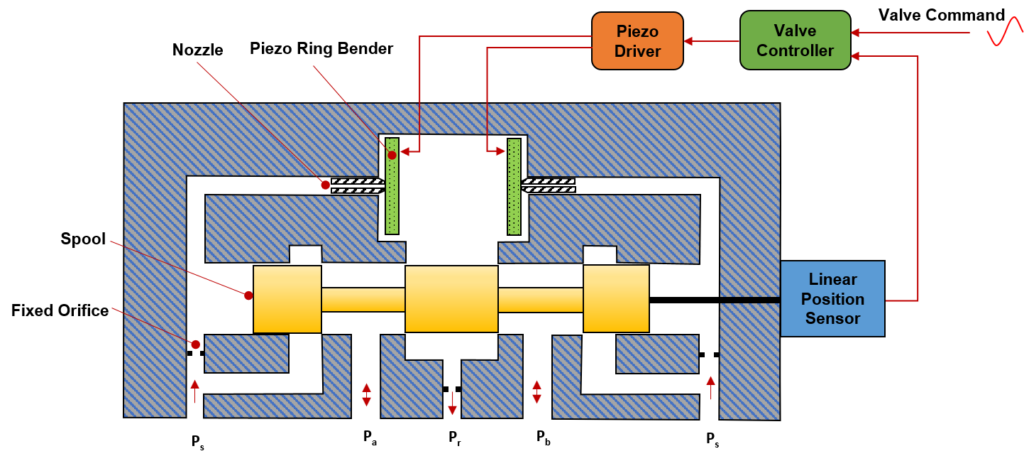
Advantages of Smart-Servo-Valve Technology
The smart-servo-valve technology provides the following unparalleled competitive advantage. One benefit is to provide a highly reliable servo valve essentially free of mechanical failures. This objective is achieved by remove the torque motor, flapper, and feedback spring and use bendable piezo members so that the servo valve first stage becomes free of moving mechanical parts.
Another benefit is to provide a highly reliable servo valve that is not prone to fluid contamination. This objective is achieved by independently restrict each nozzle, so the maximum chip shear force is available at all times and in any position.
Another benefit is to provide a highly reliable servo valve that is not prone to nozzle blockage. This objective is achieved by independently control each nozzle. The control loop will rebalance the pressure across the spool by opening up the opposite side of the nozzle, the amount defined by the size of the debris.
Another benefit is to provide a low internal leakage servo valve to minimize the continuous flow loss through the nozzles. This objective is achieved by independently restrict each nozzle, and the nozzles are closed when the valve is in a standby state.
Another benefit is to provide a servo valve free of null bias and shift. A closed-loop electrical control system on the spool position will compensate for any performance degradations and provide robust and precise servo valve control.
Another benefit is to provide a highly reliable servo valve that can operate and survive in a high g-force and high vibration environment. This objective is achieved by remove the torque motor, flapper, and feedback spring and use piezoelectric ring-benders so that the servo valve first stage becomes free of moving mechanical parts.
Another benefit is to provide a very high bandwidth servo valve. This objective is achieved by independently control each nozzle so that the fixed orifice can be sized based on servo valve bandwidth requirement.
EHSV Various Deficiencies
Electro-hydraulic servo valves (EHSV) are widely used in aerospace, earthmoving machinery, steel, power generation, chemical, and other fields. Unfortunately, the electro-hydraulic servo valve is also one of the most failure-prone components and directly and significantly impacts the entire servo control system’s performance and reliability. The significant drawbacks of the electro-hydraulic servo valve are 1) fluid contamination which can cause spool stiction, seizure, and nozzle blockage. 2) null bias or shift can manifest itself as an actuator position error. 3) significant bandwidth reduction at low temperatures. 4) high leakage or power loss due to the continuous flow through the nozzles. 5) failure modes within the torque motor section include breakdown or short circuit in the coil, faulty wires to the driver current source, imbalance in the air gaps. 6) failure modes in the flapper nozzle section include flapper erosion, broken flapper, broken feedback spring.
There has been considerable research and development work done to optimize the existing design to address various failure modes of the EHSV over the years. Unfortunately, these incremental improvements have not significantly changed the EHSV reliability and performance, and the problems are left unresolved. The fluid power industry needs smart-servo-valve technology to push forward the current state of the art and significantly improve the reliability and performance of the existing EHSV.
Conclusions
The smart-servo-valve technology addresses all deficiencies of the electro-hydraulic servo valve. It provides a technology-ready state-of-the-art solution and makes the current hydraulic servo systems significantly better.